Oxidized Polyethylene Wax (OPE)
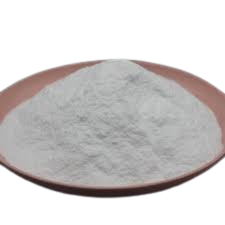
Oxidized Polyethylene Wax (OPE) is a derivative of polyethylene wax that has been treated with oxygen (oxidized) under controlled conditions. This oxidation process enhances the wax’s properties by introducing functional groups (such as carboxyl, hydroxyl, and carbonyl) onto the polymer chains. These functional groups make oxidized polyethylene wax more reactive and hydrophilic, giving it a broader range of industrial applications compared to non-oxidized polyethylene wax.
Key Characteristics:
- Appearance: Typically a white to off-white powder or granular form, depending on the processing.
- Molecular Weight: Usually higher than that of standard polyethylene wax, which increases its melt viscosity and overall performance in various applications.
- Melting Point: Generally ranges from 110°C to 130°C, depending on the grade and molecular structure.
- Solubility: Insoluble in water but soluble in hydrocarbon solvents.
- Acid Value: The oxidation process results in a higher acid value, which is an important indicator of the degree of oxidation.
- Functional Groups: Contains oxygenated functional groups like carboxyl (-COOH), hydroxyl (-OH), and carbonyl (-C=O), which give it improved reactivity compared to unoxidized polyethylene wax.
Key Properties of Oxidized Polyethylene Wax (OPE):
- Increased Surface Energy: Due to the introduction of polar groups, OPE has increased surface energy, making it more effective in applications requiring wetting, adhesion, and compatibility with polar materials (e.g., pigments, fillers, and resins).
- Improved Dispersibility: The oxidized form of polyethylene wax disperses more effectively in water-based systems and polar solvents, making it suitable for a variety of aqueous and polar solvent-based formulations.
- Lubrication & Slip: OPE offers excellent lubrication properties, improving slip and reducing friction in applications such as coatings, inks, and plastics.
- Enhanced Adhesion & Compatibility: The polar functional groups increase adhesion to substrates like plastics, metals, and textiles, improving wetting and the ability to bind materials.
- Thermal Stability: OPE retains good thermal stability, making it suitable for use in high-temperature environments without significant degradation.
- Improved Dispersion of Pigments and Fillers: Due to its polar nature, OPE is particularly useful in improving the dispersion of pigments, dyes, and fillers in coatings and paints.
Applications of Oxidized Polyethylene Wax (OPE):
Paints & Coatings:
- Acts as a dispersing agent and wetting agent in both water-based and solvent-based coatings.
- Improves scratch resistance, matte finishes, and lubricity in coatings and paints.
Ink Industry:
- Used in printing inks for improved flow, dispersion of pigments, and slip resistance.
- Improves the rheological properties and smoothness of the ink.
Plastic & Rubber Processing:
- Processing aid in plastics manufacturing, improving molding and extrusion processes.
- Enhances slip and lubrication in plastic films and molded products.
Adhesives & Sealants:
- Enhances adhesion to a wide range of substrates and improves wetting properties in adhesive formulations.
Textile Finishing:
- Applied as a softener and lubricant in textile finishing processes.
- Improves smoothness, slip, and water repellency in fabrics.
Polishes:
- Used in floor polishes and furniture polishes to improve shine and durability.
- Provides a smooth finish and enhances the non-stick properties.
Cosmetics:
- Used in cosmetic formulations (such as lipsticks and skin creams) for its emollient properties and ability to enhance texture and smoothness.
Agricultural Products:
- Used in some agricultural formulations as a dispersion agent for pesticides or fertilizers.
Advantages of Oxidized Polyethylene Wax (OPE):
- Improved Adhesion: Due to the polar groups introduced during oxidation, OPE offers superior adhesion to a wide range of surfaces.
- Enhanced Performance: Provides better dispersion, lubrication, and wetting compared to standard polyethylene wax.
- Increased Reactivity: Its functional groups make it more chemically reactive, allowing it to be modified for specific industrial needs.
- Versatility: OPE can be used in a wide variety of applications, including coatings, inks, plastics, adhesives, and textiles.